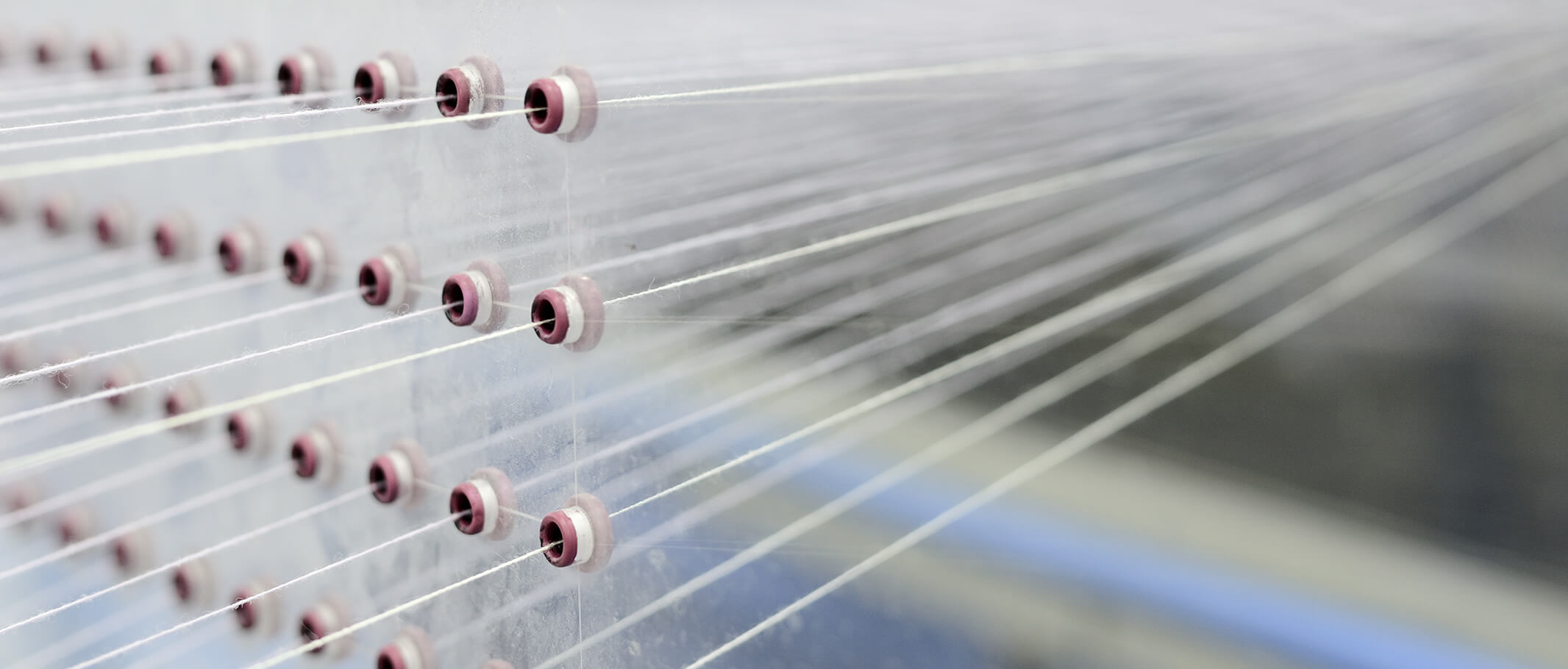
To inherit handicraft art is to inherit culture.
The lifestyle cherished and advocated by 1436,
Emphasizes sustainability, independence, confidence, love for life, and exploration of fashion and art.
The natural and rare cashmere from Arbas Baby Cashmere Goat,
Woven with exquisite craftsmanship with heart and soul,
Is presented to everyone who celebrates life,
To experience the warmth from nature and artisans.
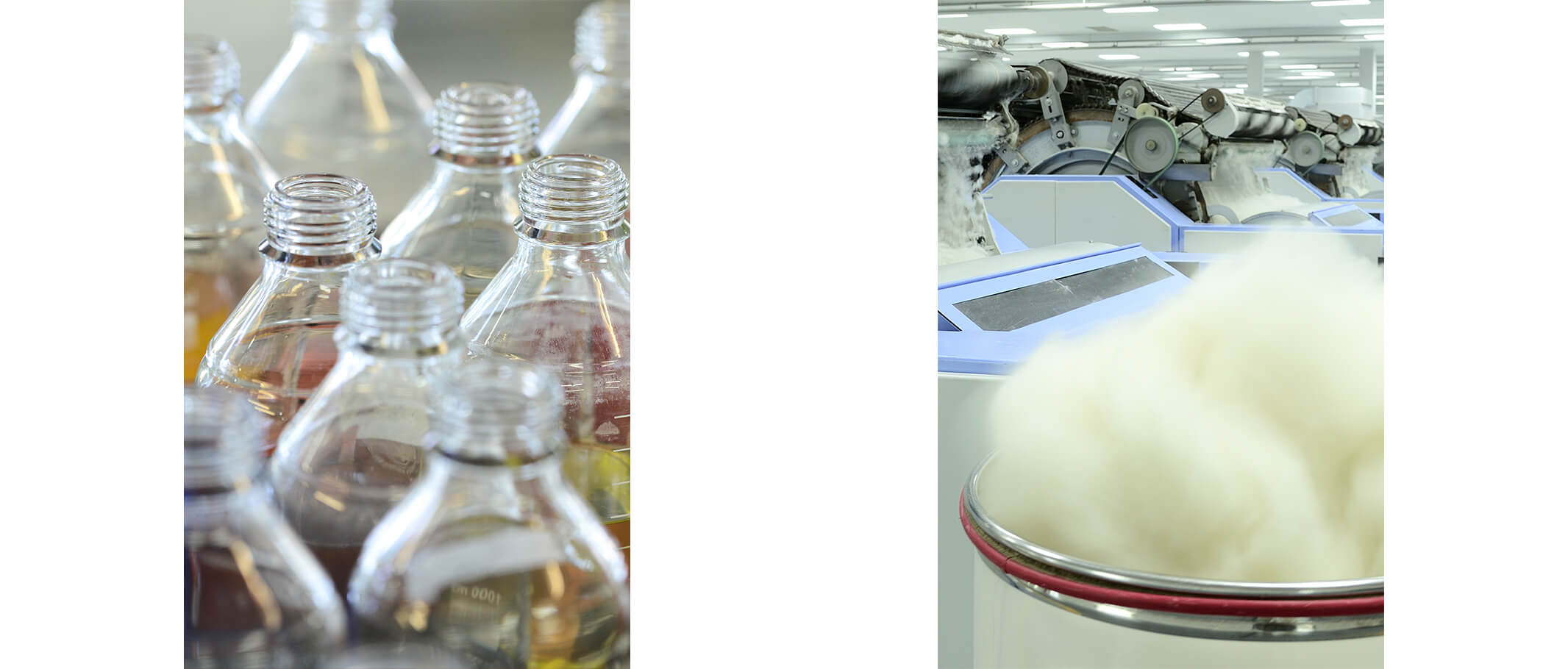
MANUAL SELECTION
Quick identification of subtle differences of raw cashmere in color is subject to both talent and experience.
Raw cashmere is generally classified by color into white cashmere, green cashmere and brown cashmere that are from different breeds of cashmere goats, white ones, green ones (brown ones) and black ones. Among them, white cashmere has the best quality, while green cashmere is long yet coarse, and brown cashmere has long and fine fibers, but its dyeing is generally restricted.
Raw cashmere of 1436 only chooses that from Arbas Baby Cashmere Goat and is manufactured into white of white cashmere that is light as clouds, white as snow and soft as silk after manual selection and dehairing. Foreign matters including burrs, paints, dark fibers, and chemical fibers of nylon bags contained in raw cashmere should be removed; however, such process can never be done by machines but by humans, for it is the first line of defense in quality control. Experienced masters identify qualified raw cashmere with perfect hand-eye coordination and a strong ability to distinguish fibers.
DEHAIRING
Dehairing is an operation to maintain the adhesion of cashmere fibers by adding moisture back to fibers, so as to remove coarse hair and foreign matters.
The washed raw cashmere is to be dehaired by machines to completely get rid of guard hair and impurities. The more times raw cashmere is dehaired, the purer cashmere fibers are. According to the standards adopted by 1436, raw cashmere should be dehaired for at least seven or eight times until light and pure white dehaired cashmere is obtained. Workers need to oversee the operation of machines and check if the cashmere in dehairing machines is to dry. If it is, they should moderately spray little water on cashmere to keep its fibers from being damaged. Such skill lies in experience. Dehairing maintains a strict standard of the purity of cashmere.
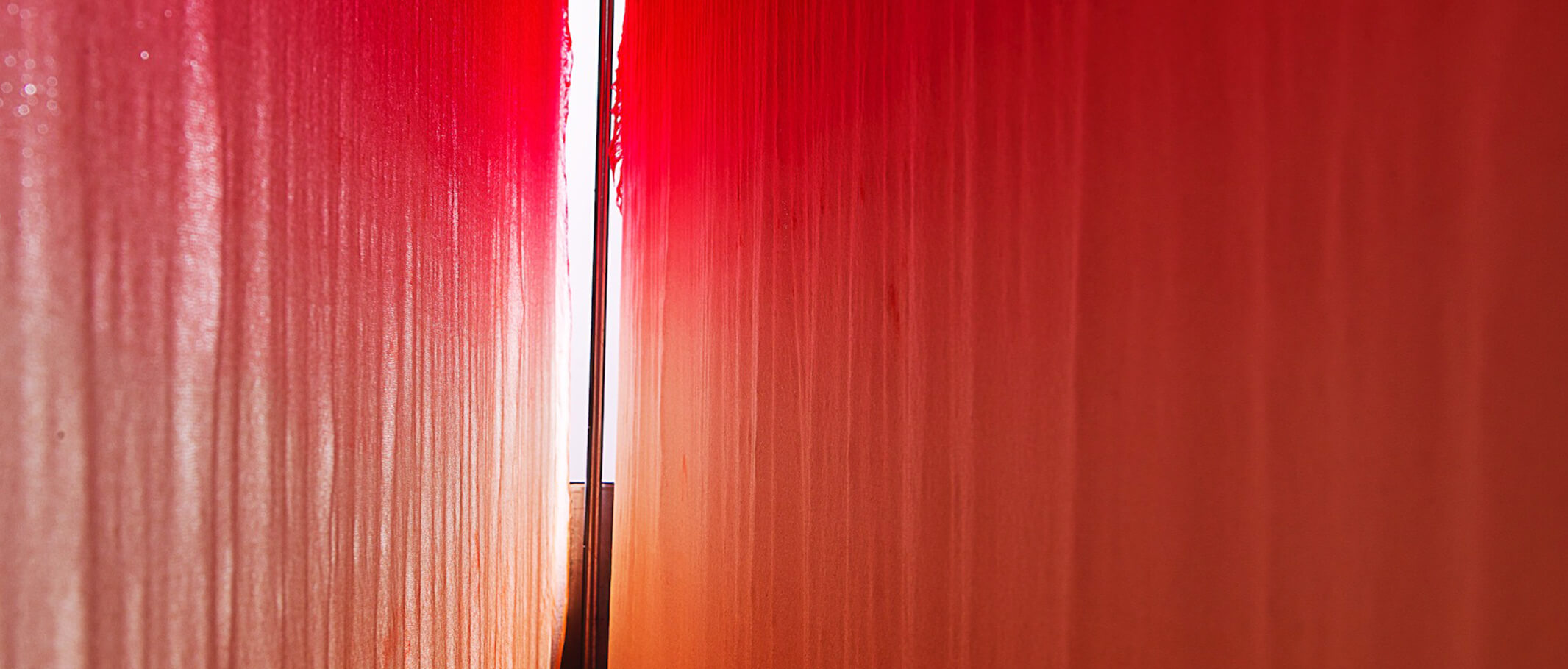
SLIVERING
Slivering is a process to sort materials and prepare your cashmere for dyeing, and it matters much for our unremitting pursuit of perfection.
Loose dehaired cashmere is sorted into slivers, which makes it convenient for gilling machines to produce worsted yarn and for dyeing. A tube can be put into the hollow inside of the cocoon-like cashmere ball so that the dye penetrates evenly into cashmere in the dye vat. This seemingly insignificant step, instead, proves the most rigorous and careful consideration of the next steps.
DYEING
Dip dye is a challenge for masters to control the time of dipping, and even one second can make a huge difference in color.
The dyeing and finishing process can make cashmere have bright colors. 1436 employs natural and non-stimulant environmentally friendly dyes and then develops more than 400 colors especially for cashmere. The ecologically friendly dyeing process at low temperatures guarantees the natural softness and elasticity of fibers and gives Arbas Baby cashmere fresh and bright colors as well.
SPINNING HIGH COUNT
The pursuit of the ultimate is a never-ending journey.
Worsted yarns, produced by the worsted spinning system, require high-quality materials. 1 gram of 1436’s cashmere yields 100-meter long superfine worsted yarn, with even 120 counts, and even 200-meter long with water-soluble fibers. The finer and softer the fiber, the higher the count. The Technology Center of 1436 has been developing a super light 230-count product, with the hope of setting new international standards. What drives the continuous improvement of spinning technology is our insatiable desire for breakthroughs.
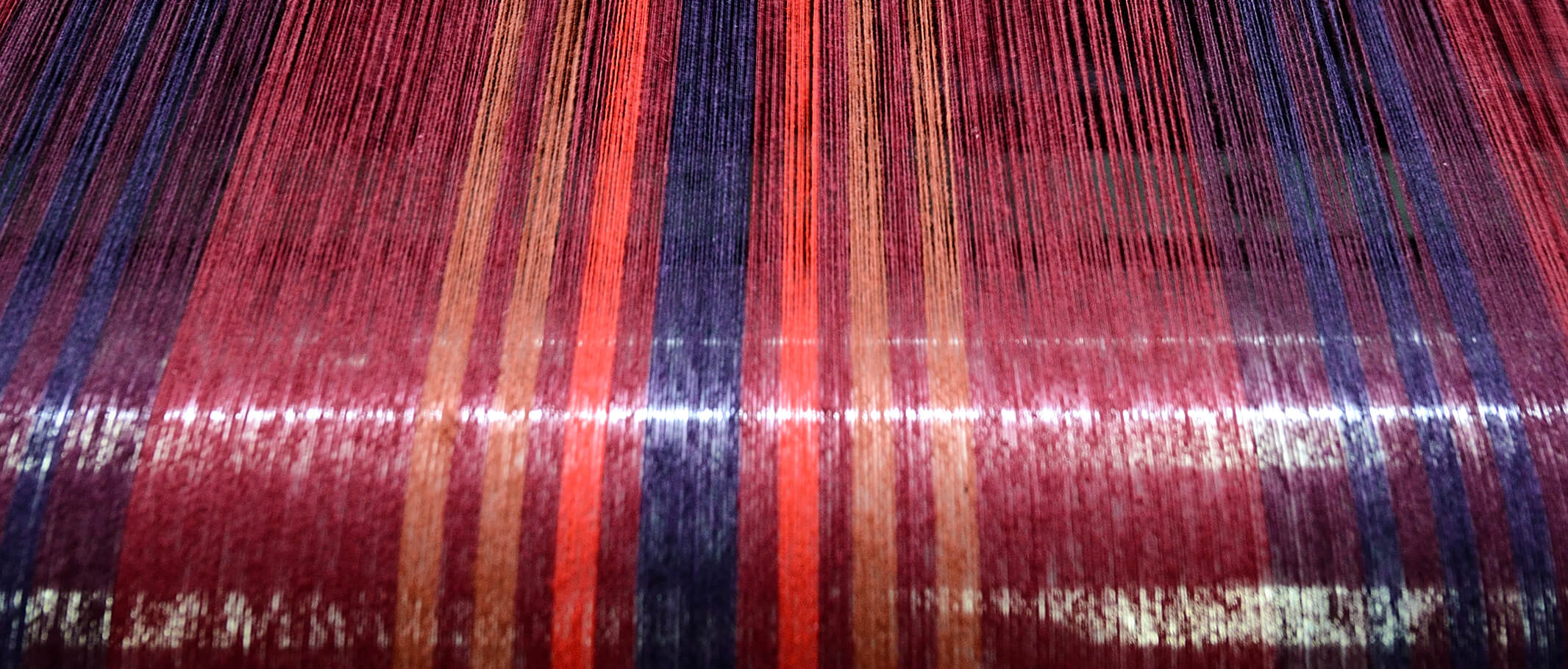
MANUAL DRAFTING
The tedious process is endowed with the dynamic beauty thanks to patience.
The warp is to pass through a heddle according to the arrangement requirements, which is done manually. Such handwork can never be replaced by machines, highlighting the precious and invaluable craftsmanship. For a simple arrangement, 5000 warp threads can be drafted every day. Each warp needs to be drafted before it is ready for the loom. The process requires both excellent skills but also conscientious meticulosity for even a minor failure can lead to the disqualification of the whole cloth. The craftsmen move their fingers fast as if they are playing emotional piano songs. The beautiful and attractive piece is the outcome of repeated rehearsals. Behind the seemingly monotonous repetitions, there is longtime persistence and disinterested concentration.
WEAVING
Yarns or threads are interlaced to form a fabric or cloth, which stands at the intersection of craftsmanship and technology. Weaving is a dialogue between yarns and cloth. Yarns move, interlace or encircle in the same direction to present themselves with structures for clothing. The two techniques, knitting, and tatting create different feels and are the soul of design details. Fully fashioned weaving and ADF technology are currently top weaving techniques. Fully fashioned computerized weaving is a technique which can shape a fabric with one yarn without seams, while ADF computerized weaving can produce individual pieces of cloth, such as front parts, back parts, sleeves, and necklines. Cashmere is invested with countless new possibilities by the language of technology, fabrics, and structures.
TRADITIONAL PRINTING
There are no challenging printing plates but picky craftsmen. Screen printing not only maintains the proper temperature and traditional skills but also makes the prints more stereoscopic. The yarn for plate making must be 120 mesh, the larger the number, the smaller the mesh. Before printing, workers check whether there are defects other than patterns and if so, they block them with photosensitive glue to avoid dyeing. Separated colors are printed one by one, and one color of the graphic is printed with an individual plate, therefore it is possible to print a complicated graphic on fabric by up to 20 plates.
MANUAL JACQUARD WEAVE
Each piece of clothes shines forth with unique beauty from the slight and subtle differences. Even though machines can produce more complicated jacquard graphics, wisdom passed down by craftsmen is retained in 1436. Despite their different methods and techniques, craftsmen can finish the same jacquard, which extends the life of skills. The difference brought by pure handwork gives each piece of clothes a distinct soul. It takes dozens of hours or event two weeks for the most experienced craftsmen to complete the jacquard of one part, which is an unprecedented test for patience and concentration.
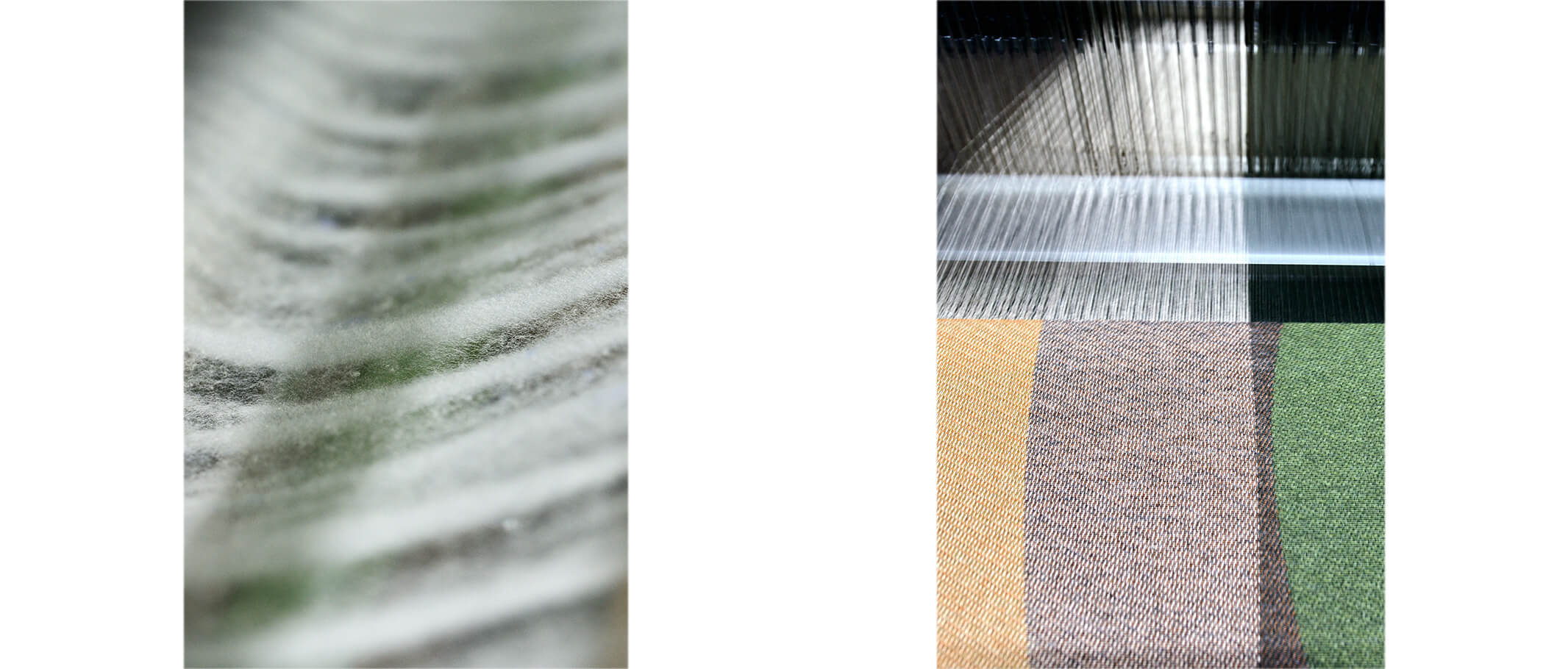
MANUAL EMBROIDERY
The most traditional craftsmanship comes from the degree to which handwork and fabrics coincide with each other. Such exquisite operation must only be completed by experienced craftsmen. Pattern sheet is put over the cloth for the craftsman to refer to. Every stitch stands in need of concentration without any hesitation, and only by following regular patterns can craftsmen create smooth and even lines. Stitch threads with embroidery needles for the glorious, brilliant and fashionable clothes, the graphics of which shine a new life with the temperature of hands.
HANDMADE DOUBLE-SIDED COAT
Even the most accurate machine can never replace the exquisite craftsmanship and wisdom from experience. The handmade double-sided coat seems a naturally integral whole without any noticeable pinhole or thread residue. Two thin pieces of cashmere cloth are sewn into a breathable coat by cutting and hand-sewing. The dense and even stitch pattern is a test for the craftsman to produce warm coats with unique characters.
MANUAL LABEL APPLICATION
It is a moment when countless ingenue craftsmen and artisans show their persistence. Label application is a vital imprint of 1436. Our commitment to green nature is expressed through the handwork. Natural cashmere brings comfortable experience for wearers, and the environmentally friendly raw materials do not add to the burden of the Mother Earth. The completion of each cashmere product is a combination of green manufacturing and handwork so that consumers can feel the warmth from the blessings of nature.